
Manufacturing accounting
Helping you manage manufacturing operations
Today’s manufacturing industry is intensely competitive. Pulse manufacturing accounting solutions can be invaluable to your business.
From the advice to the financial services we have to offer, we can support you in ensuring everything is in order for optimal business growth.
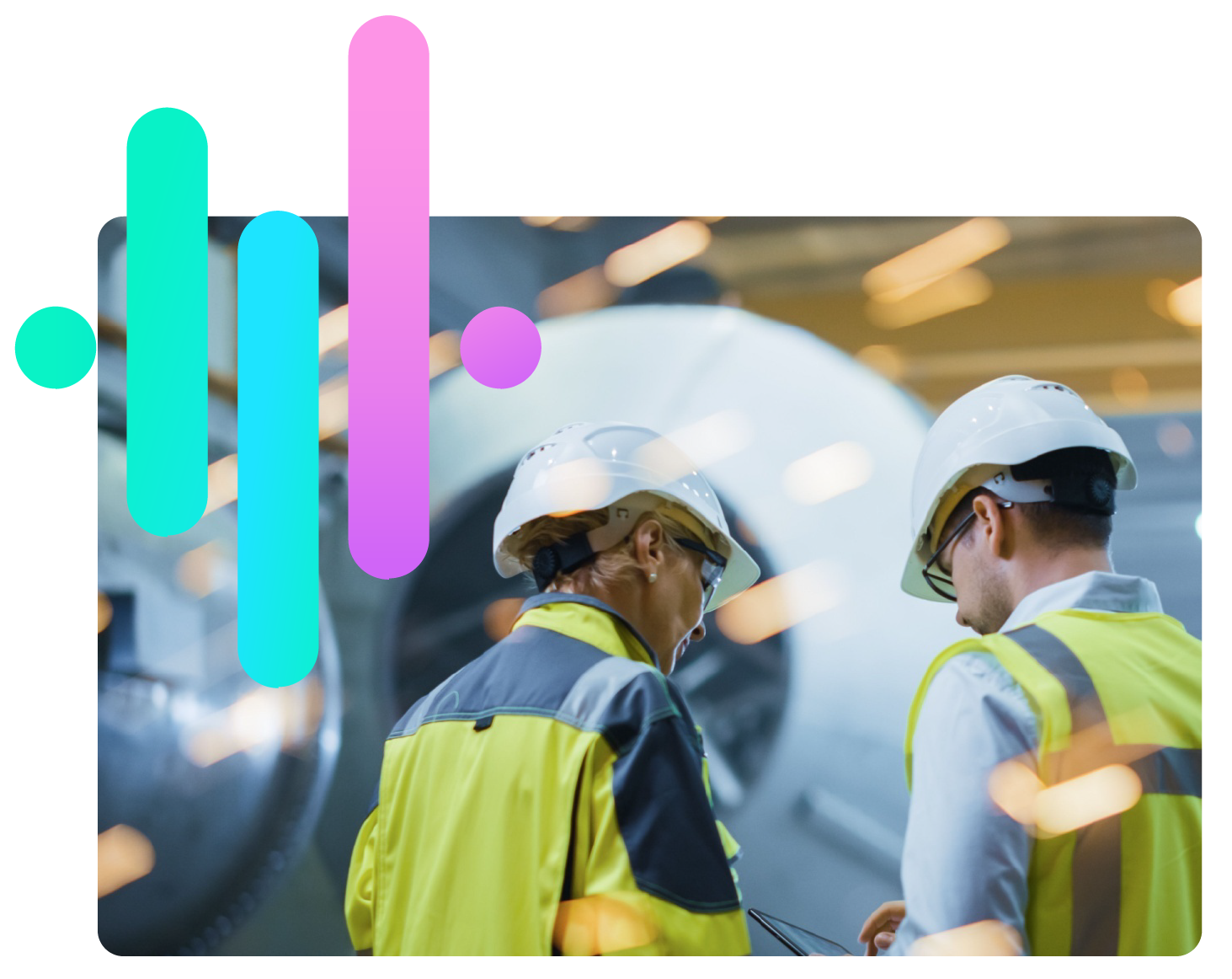

Services
What We Do
- Accounts Preparation
- Bookkeeping
- VAT
- Management Accounts
- Payroll
- Construction Industry Scheme
- Cloud Accounting Advisory
- Forecasting
- Business Advisory
- Tax Advisory & Tax Investigations
- R&D and other Tax Reliefs
- Business Growth & Finance Raising
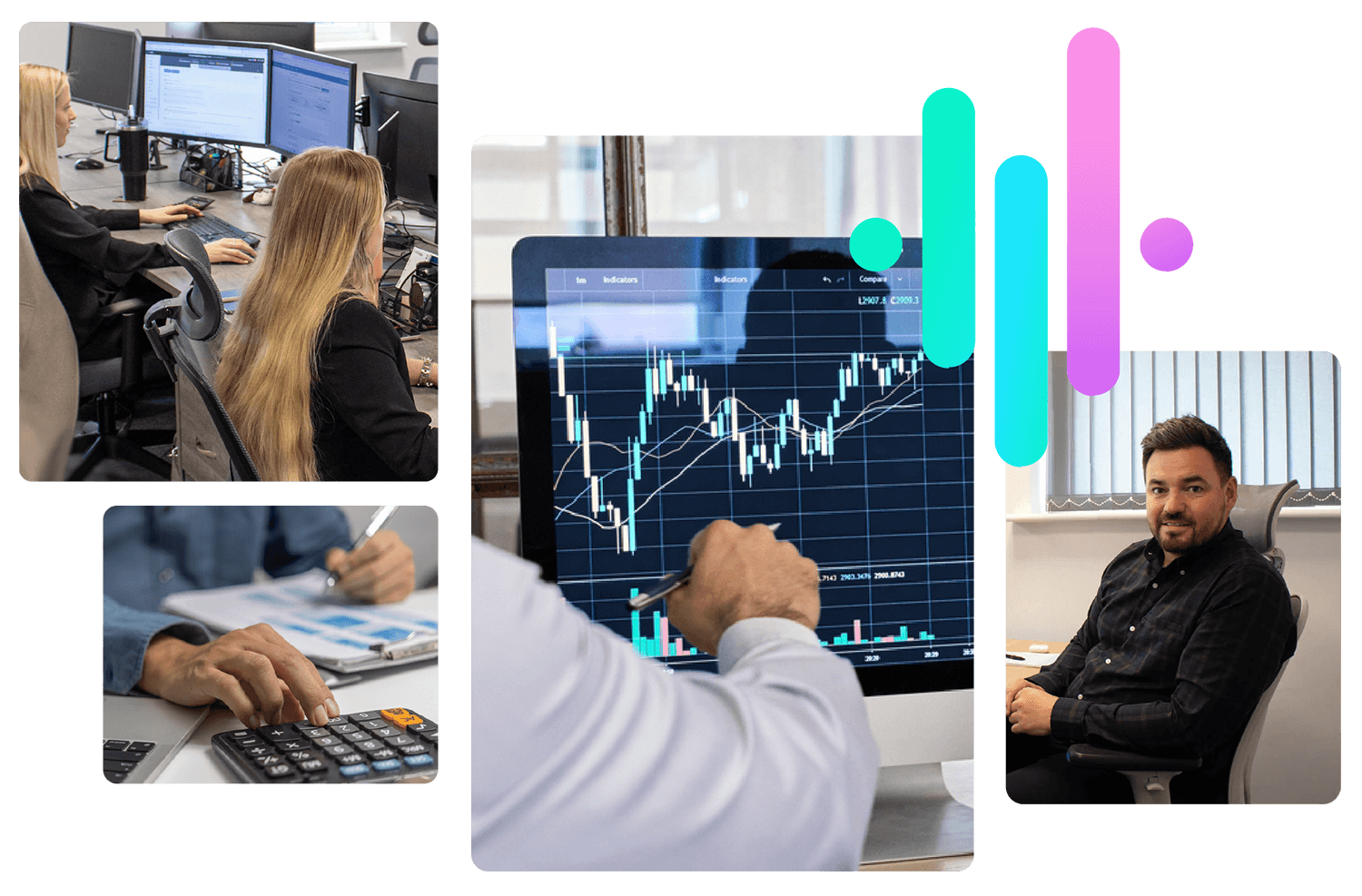

Reach optimal growth with
manufacturing accounting
Our team of manufacturing accounting specialists is dedicated to helping you reach your goals. Whether you need practical advice, tax support or help with tidying up your financial performance and accounts, Pulse can be your go-to.
As manufacturing accountants, we can help you keep track of cost of production, cost of good sold (cogs), cost of goods manufactured (cogm), direct labor costs, and even indirect costs.
Expert Accountants
Our aim is to offer our clients a fresh approach to managing their finances. With 132 years of combined accounting experience, we can guarantee expert guidance tailored to your needs.
Personal Relationships
We don’t believe in a ‘one-size fits all’ approach. Instead, we aim to cultivate meaningful connections that enable us to provide tailored solutions that actually make a difference.
Competitive Prices
At Pulse, we offer competitive prices for high-quality services. Our pricing structure is designed to be transparent and straightforward, ensuring there are no surprises with fixed costs.

Manufacturing Accounting Services
The most popular manufacturing accounting services for those in the manufacturing industry include:
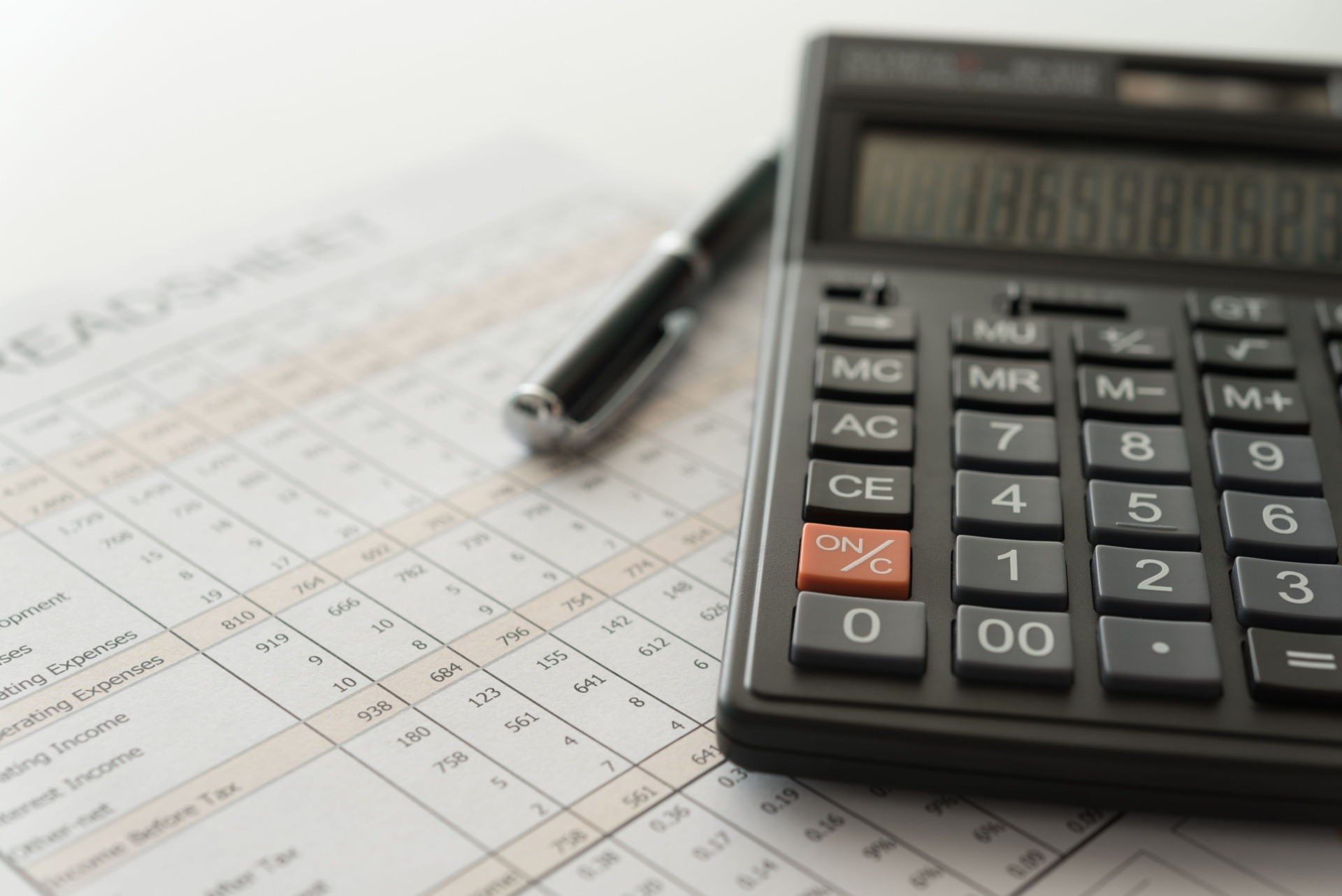
Accounting
Our manufacturing accounting service delivers reliable solutions to streamline your financial processes. From managing production costs to preparing accurate financial statements, we help manufacturing businesses stay compliant and maintain financial clarity.
Find Out More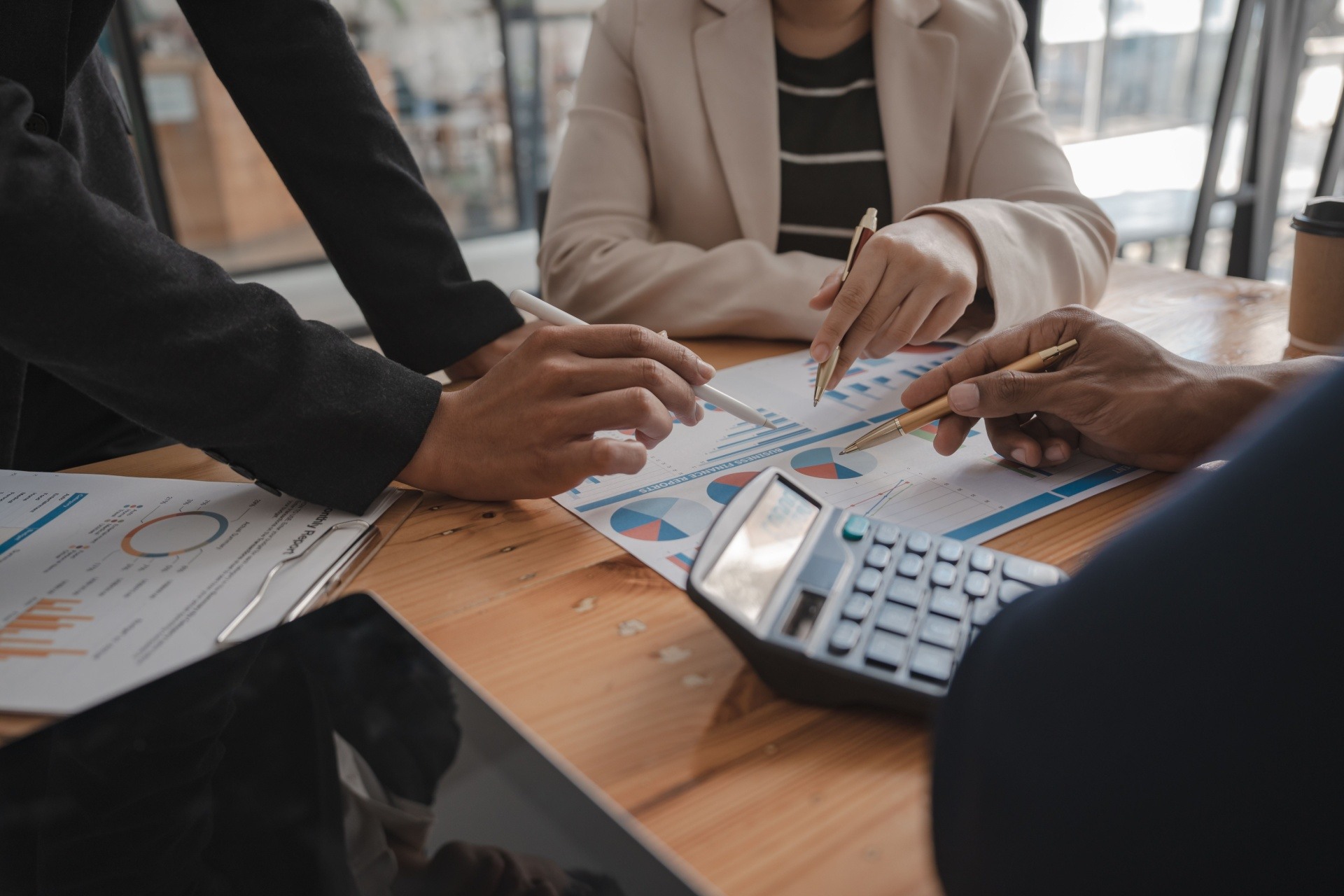
Tax Advisory
Manufacturing businesses face unique tax challenges, and our expert tax advisory services provide tailored guidance to help you minimise liabilities and maximise savings. From VAT strategies to capital expenditure planning, we ensure your tax planning is industry-specific and efficient.
Find Out More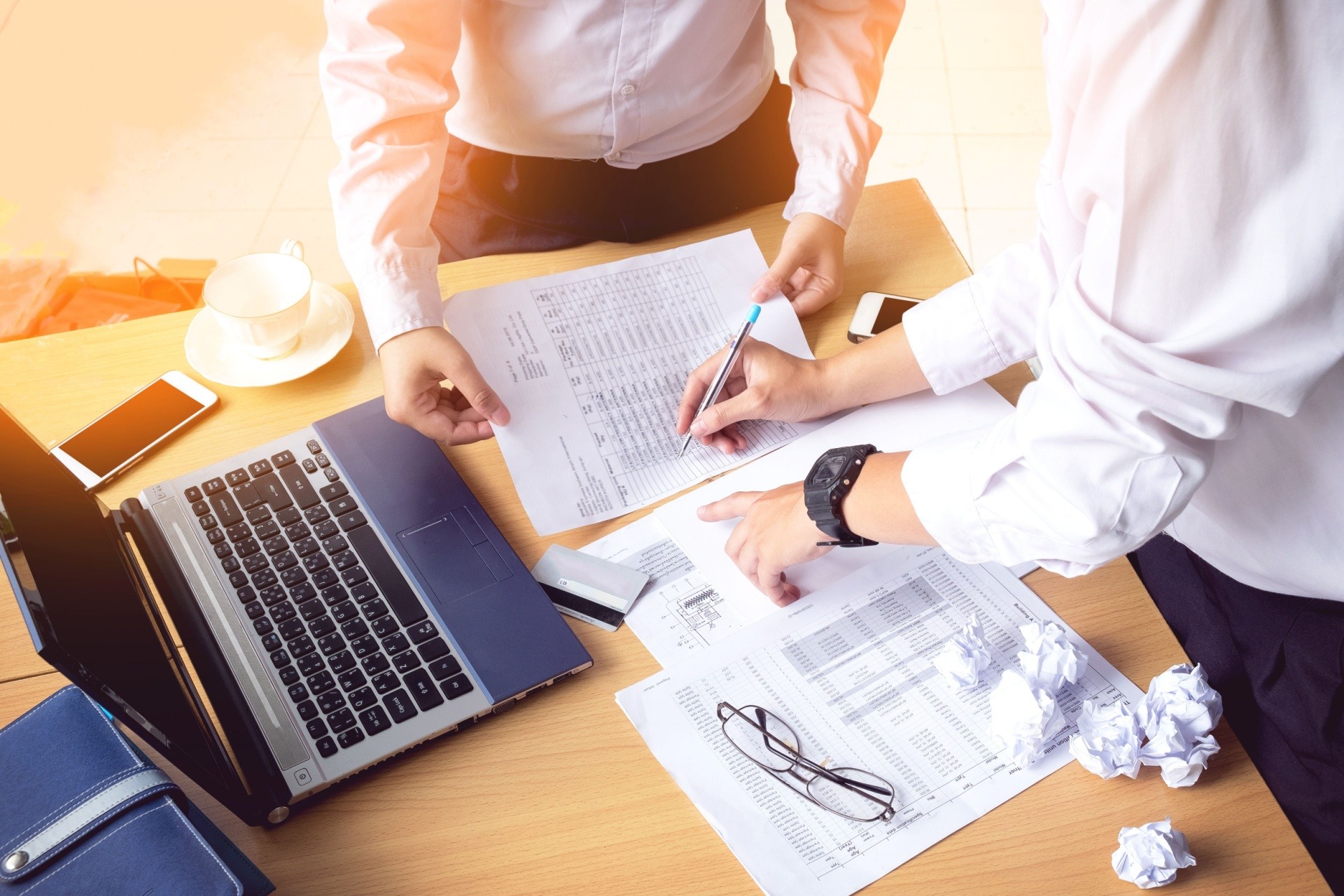
Payroll
Pulse Accountants provides efficient payroll solutions tailored to the needs of manufacturers, including handling variable shift patterns, overtime, and tax compliance. Our experts ensure your workforce is paid accurately and on time, so you can focus on production.
Find Out More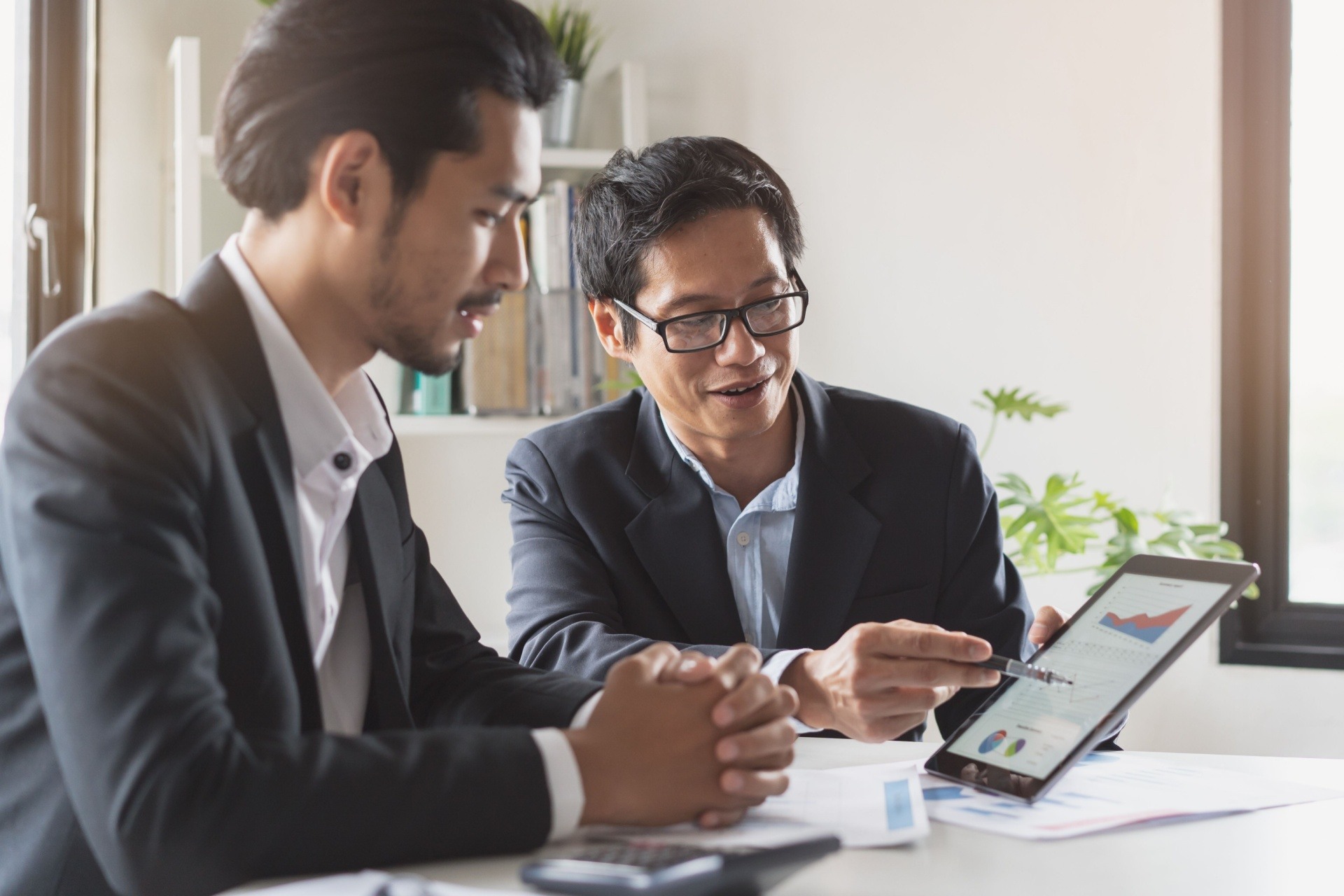
Business Advisory
Our business advisory service for manufacturers is designed to enhance growth and profitability. From improving cash flow to strategic planning and inventory, we offer tailored advice to help you optimise operations, manage finances, and seize new opportunities in the manufacturing sector.
Find Out More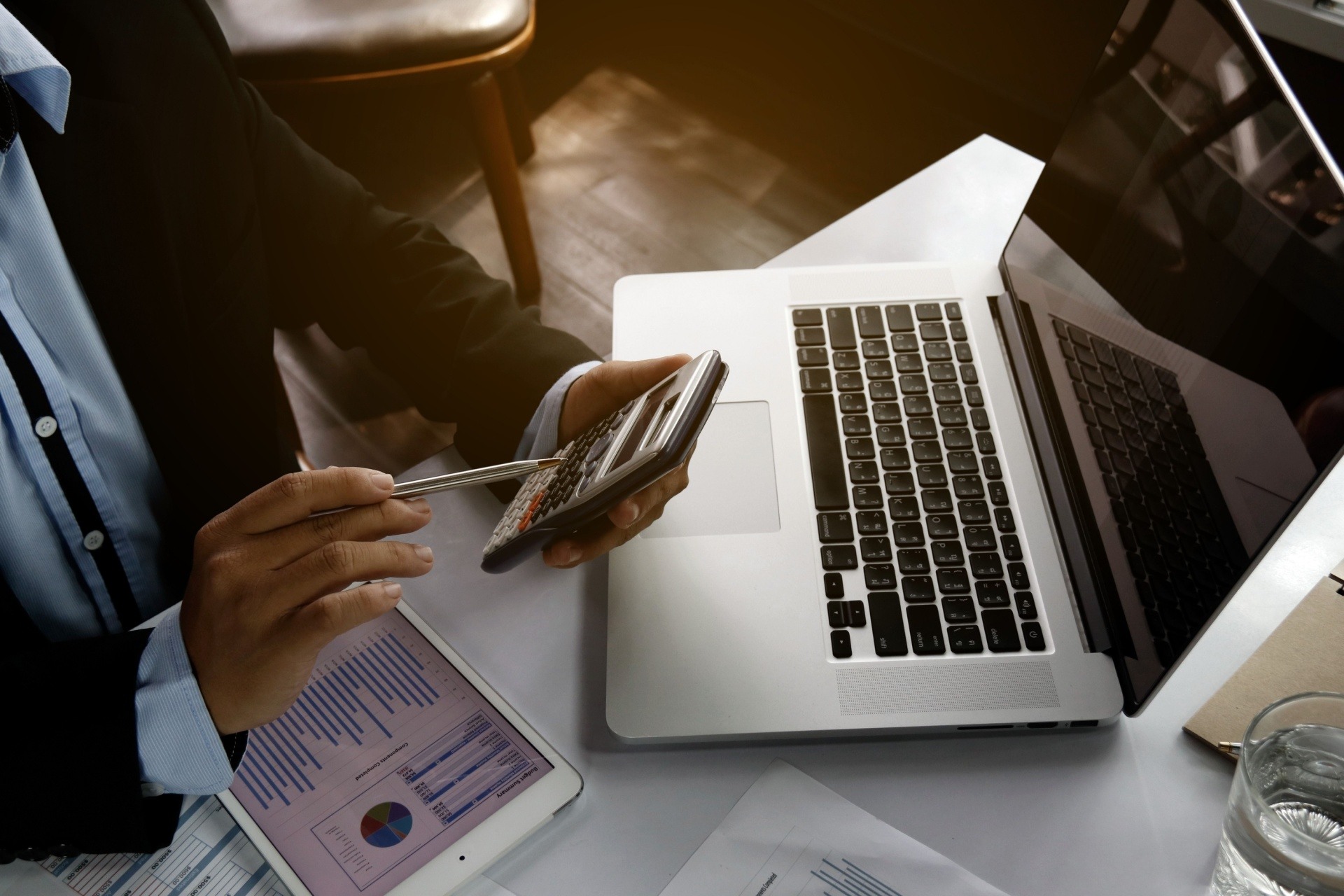
VAT
Navigating VAT in the manufacturing industry can be complex, but our expert team simplifies the process. We ensure compliance with VAT regulations while helping you optimise VAT recovery on raw materials and streamline reporting, keeping your business financially secure.
Find Out More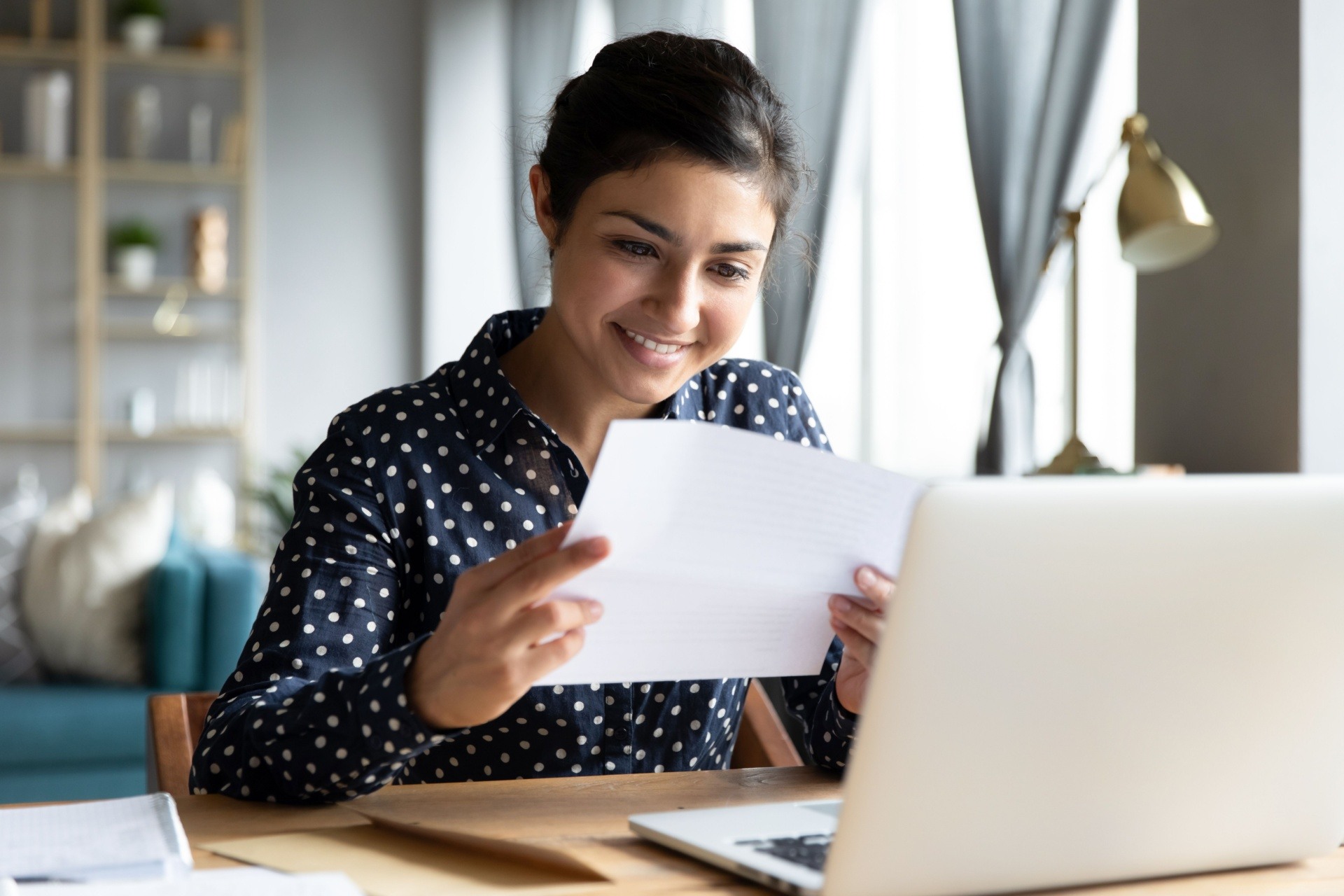
Tax Relief
Pulse Accountants can help manufacturers identify eligibility for tax reliefs, including capital allowances, R&D tax credits, and more. We’ll guide you through the process, ensuring you benefit from all available savings and reduce costs effectively.
Find Out More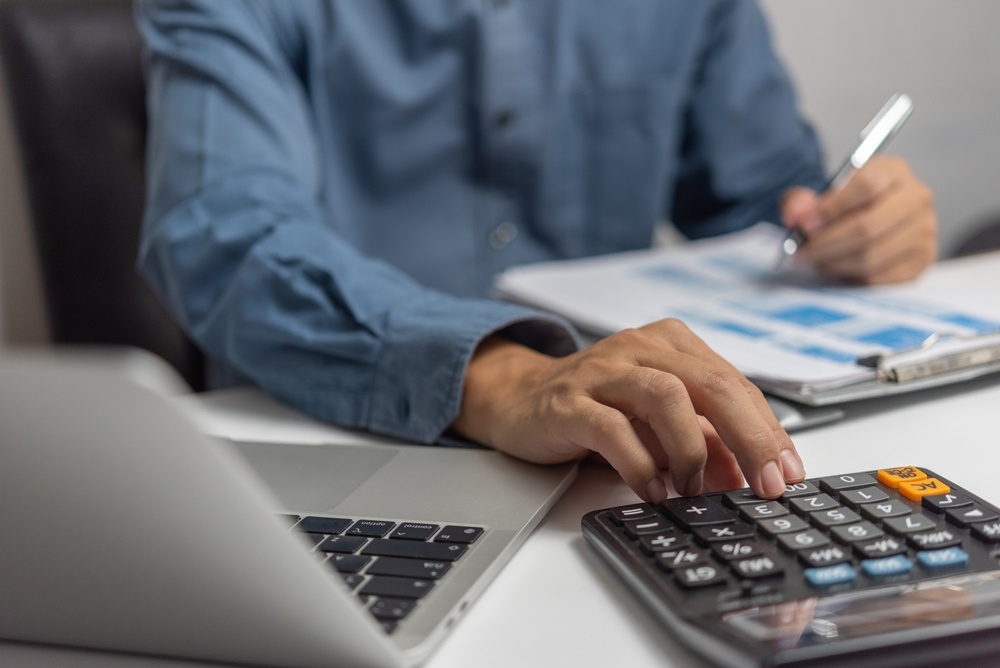
Credit Control
Effective credit control is critical for manufacturers to maintain cash flow and reduce late payments. Our customised solutions help you track receivables, manage credit terms, and improve customer relationships, ensuring your finances remain on track.
Find Out More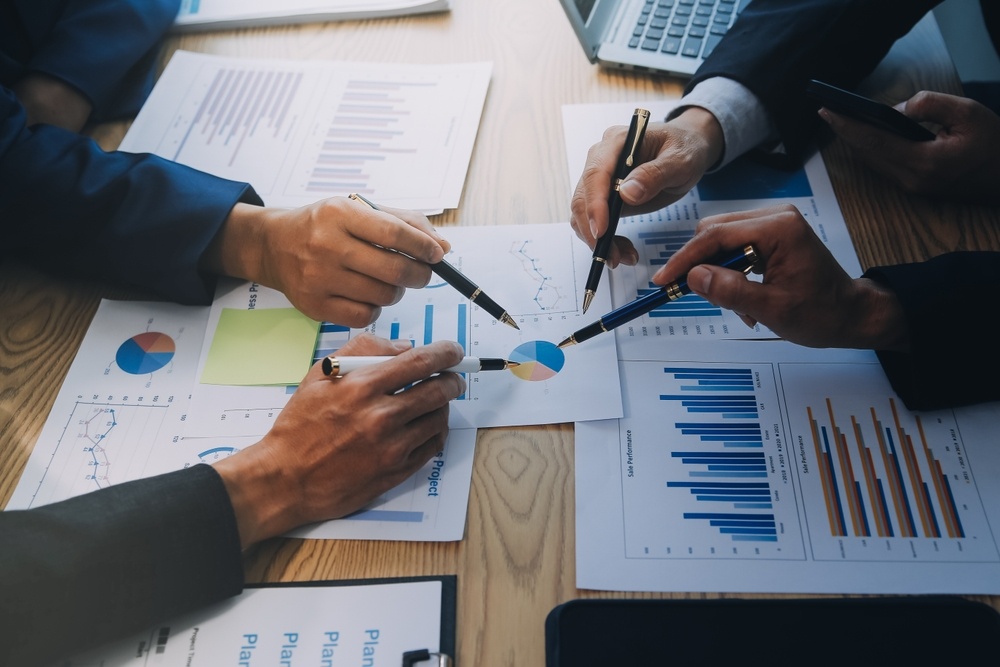
Management Accounts
Manufacturing businesses benefit from our tailored management accounts, offering insights into cash flow, profitability, and production efficiency. Our detailed reports help you track trends, compare budgets, and make data-driven decisions to drive growth.
Find Out More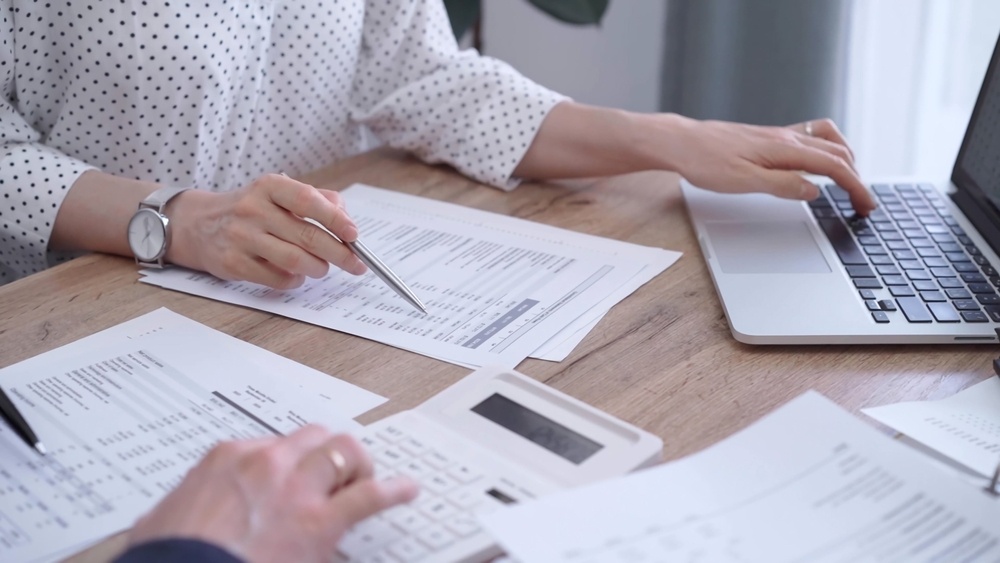
Bookkeeping
Outsource your bookkeeping to Pulse Accountants and let us handle your manufacturing-specific needs, from tracking production costs to reconciling accounts. Using modern technology, we ensure accuracy and efficiency, so you can focus on growing your manufacturing business.
Find Out More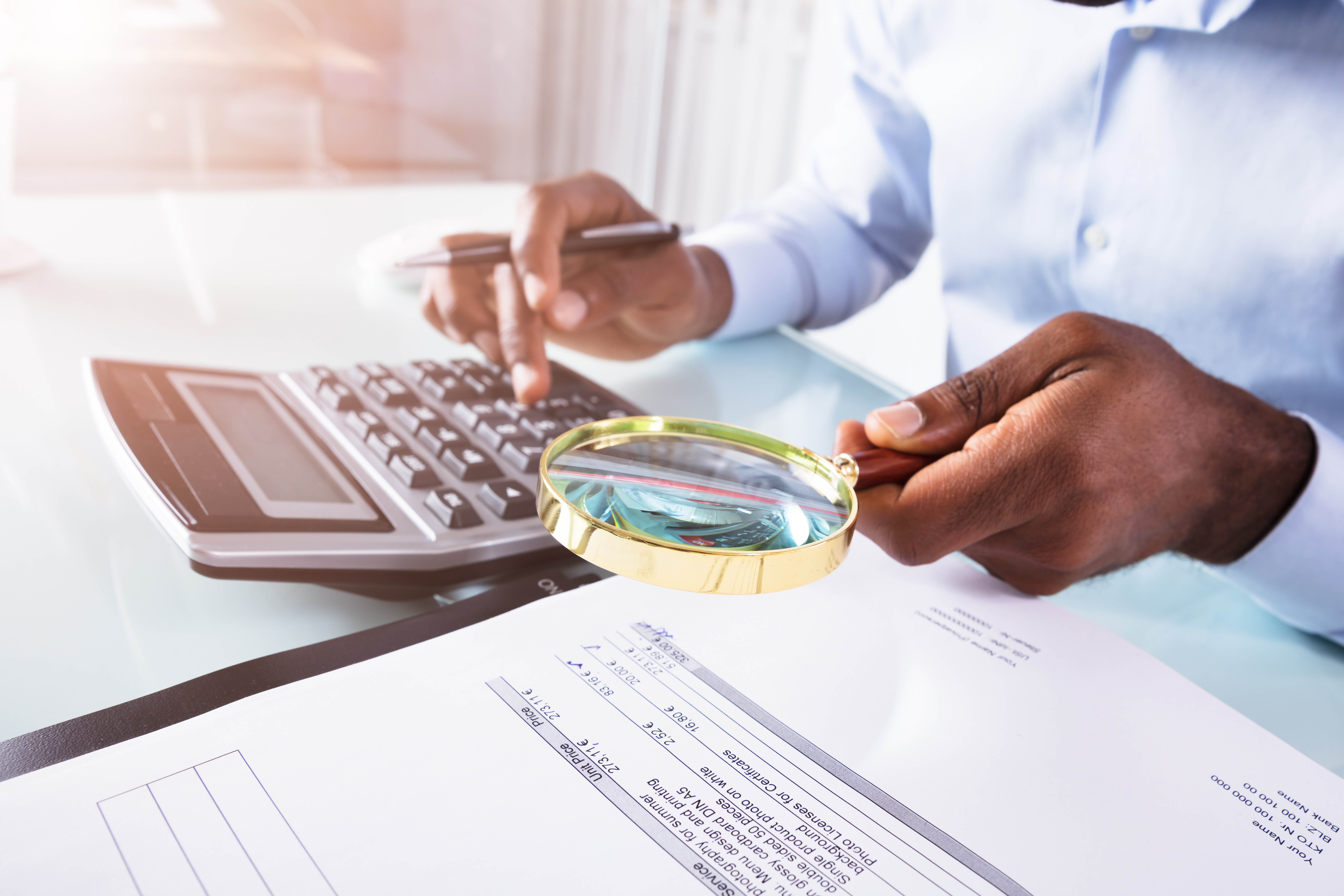
Tax Investigations
Our tax investigation insurance provides peace of mind in the event of an HMRC enquiry. This service covers the professional fees involved in responding to investigations, whether routine or complex. It ensures that you’re supported throughout the process, helping to minimise disruption to your manufacturing process and manage the situation with confidence.
Find Out More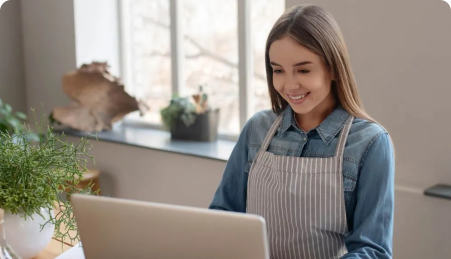
Salary Sacrifice
Our salary sacrifice service helps implement tax-efficient employee benefits schemes in manufacturing businesses. By exchanging part of an employee’s salary for non-cash benefits, both employers and staff can reduce National Insurance costs. We ensure each scheme is fully compliant and aligned with your specific manufacturing business goals.
Find Out More90%
Companies using accounting services reduce their manual data entry errors by 90%
40%
Less than 40% of businesses that use excel for their finances are happy with their existing accounting processes
41%
Error from unqualified individuals accounts for 41% of inaccurate numbers in reporting
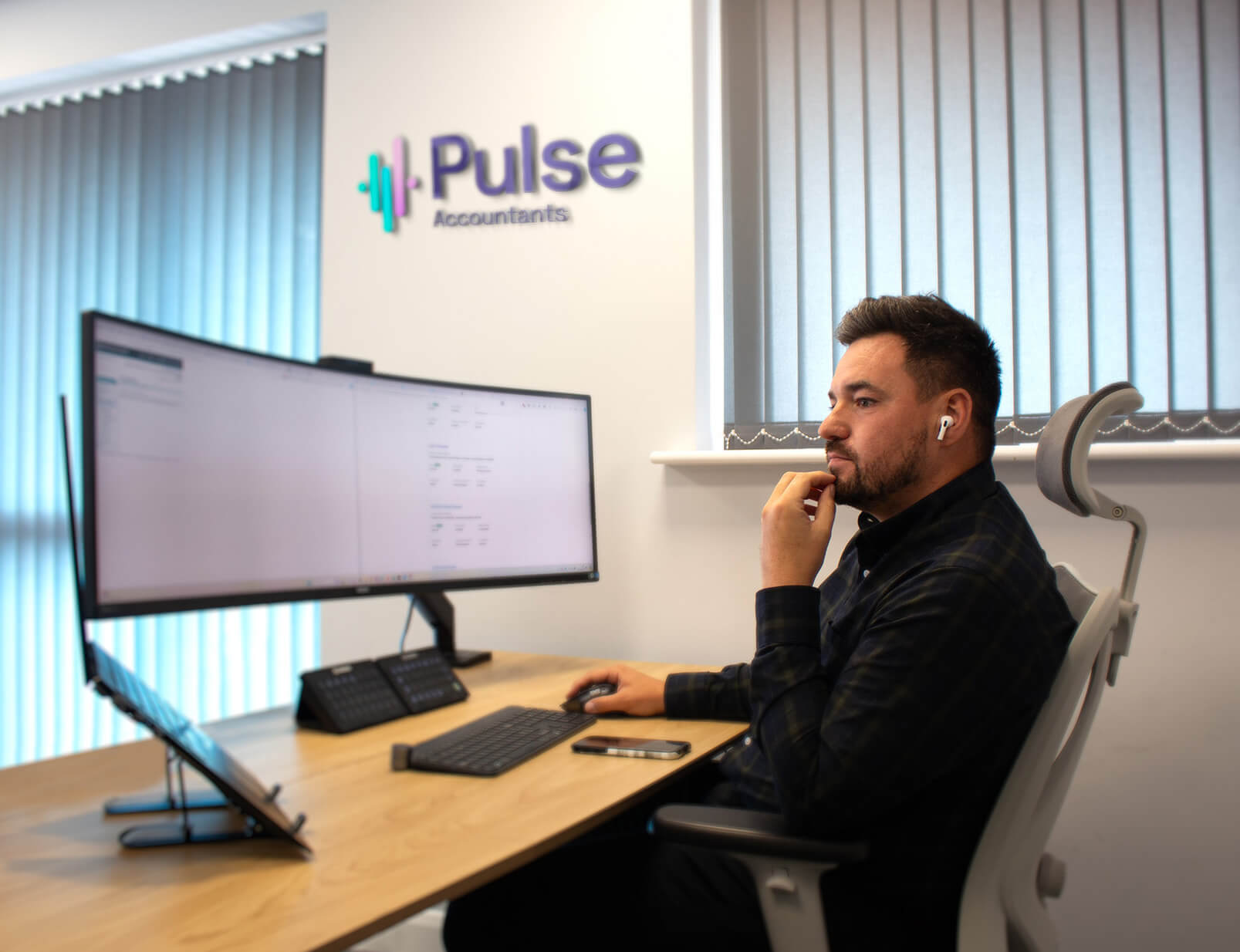
Why Choose Pulse Accountants?
We want to share Pulse and create connections with businesses and potential clients alike. We are here to help you keep your finger on the Pulse of your accounts.”
Matthew McConnell
Founder and CEO
Pulse Accountants
Customers reviews
We’ve been using Pulse for our accounting services for several years now, and have just always had exceptional service. The onboarding was seamless, and their support has been invaluable and the team are always on hand for any questions. They have genuinely taken a lot of stress away from our team and truly simplified our end-to-end accounting needs.
Laura Davis, Finance Manager
Growth Capital Ventures
I can fully recommend Pulse Accountants for their outstanding accounting services. What truly sets them apart is how they have demonstrated a deep understanding of our business needs from the onset and tailored their approach to suit our requirements as a training business with funding contracts. Their expertise in tax planning saved us a significant amount of money, and their clear, timely financial reporting has empowered us to make informed decisions confidently.
Ian Nelson, Co-Founder
NC Group Ltd
The team have supported the expansion of my property portfolio providing high class advice which has driven my company to become a success. Pulse Accountants have taken our new company Synergy Wind Management to the next level, designing a bespoke management and payroll system. The high level service, professionalism and personal touch Pulse Accountants push to achieve year on year is truly outstanding. I'd certainly recommended Pulse Accountants based on my experience. This is one supplier where you won't feel like your simply just a number.
Jonathan Chung
Synergy Wind Management Ltd
Pulse have provided an excellent service level on each engagement and discipline, be it accountancy, finance or business advice. The personalised / bespoke support that Pulse has provided throughout our partnership has been a significant differentiator to set them apart from the norm. Response times are very good. As a small business owner, this level of coverage and support is essential to allow me to focus on the core business, knowing that Pulse have my back. The overall experience of being a customer with Pulse has been excellent. The specific feature worthy of recognition has been the account management role.
Derry O'Kelly, Director
MEP BID Management Limited
1. What is manufacturing accounting?
Manufacturing accounting refers to the specialised branch of accounting that focuses on tracking and managing the financial aspects of manufacturing operations. It encompasses the recording, analysis, and reporting of costs associated with the production process, including raw materials, labour, and overheads.
This form of accounting is crucial for determining the cost of goods manufactured (COGM) and the cost of goods sold (COGS), which are essential for pricing strategies and profitability analysis.
By accurately capturing production costs, manufacturing accounting enables businesses to assess their financial performance, make informed decisions, and maintain compliance with financial regulations. It also involves inventory management, ensuring that stock levels are optimised to meet production needs without incurring unnecessary holding costs.
Effective manufacturing accounting provides a clear picture of a company's financial health, supporting strategic planning and operational efficiency.
2. How does manufacturing accounting differ from other types of accounting?
Manufacturing accounting differs from other types of accounting primarily due to its focus on the production process and the associated costs. Unlike service-based or retail accounting, which may deal predominantly with straightforward transactions, manufacturing accounting must account for multiple stages of production. This includes tracking raw materials, work-in-progress, and finished goods inventories.
Additionally, it involves allocating direct and indirect costs to products to accurately determine production expenses. Manufacturing accounting also requires the implementation of complex cost accounting methods, such as job order costing or process costing, to accurately assess product costs and profitability.
This level of detail is essential for manufacturers to understand their cost structures, set appropriate pricing, and identify areas for cost reduction and efficiency improvements.
3. Why is accurate cost allocation important in manufacturing accounting?
Accurate cost allocation is vital in manufacturing accounting because it ensures that all production costs are properly assigned to the products being manufactured. This includes direct costs like raw materials and labour, as well as indirect costs such as factory overheads. Proper cost allocation allows businesses to determine the true cost of producing each item, which is essential for setting competitive prices and assessing product profitability. Misallocation can lead to distorted financial statements, misinformed decision-making, and potential losses. By implementing robust cost allocation methods, manufacturers can gain insights into their cost structures, identify inefficiencies, and make informed strategic decisions to enhance profitability.
4. What are the common challenges in managing inventory for manufacturing businesses?
Managing inventory in manufacturing businesses presents several challenges, including accurate tracking of raw materials, work-in-progress, and finished goods. Inaccurate inventory records can lead to production delays, stockouts, or excess inventory, all of which impact profitability. Additionally, valuing inventory correctly is crucial for financial reporting and tax compliance.
Manufacturers must also manage the risk of inventory obsolescence, especially in industries with rapid technological changes. Implementing integrated inventory management systems and adopting best practices in inventory control can help address these challenges, ensuring optimal stock levels and efficient production schedules.
5. How can manufacturing businesses improve cash flow management?
Improving cash flow management in manufacturing businesses involves several strategies. Firstly, optimising inventory levels to avoid tying up excessive capital in unsold goods is essential. Implementing efficient invoicing and collections processes ensures timely receipt of payments.
Negotiating favourable payment terms with suppliers can also aid in maintaining a healthy cash flow. Additionally, regular cash flow forecasting allows businesses to anticipate and plan for future financial needs.
Utilising financial management software can provide real-time insights into cash positions, enabling proactive decision-making to address potential shortfalls or invest surplus funds effectively.
6. What role does technology play in modern manufacturing accounting?
Technology plays a pivotal role in modern manufacturing accounting by automating complex processes and providing real-time financial insights.
Enterprise Resource Planning (ERP) systems integrate various business functions, including accounting, inventory management, and production planning, into a unified platform. This integration enhances data accuracy, streamlines operations, and facilitates informed decision-making.
Advanced analytics tools enable manufacturers to analyse cost patterns, forecast financial outcomes, and identify areas for improvement. Cloud-based accounting solutions offer scalability and remote access, allowing for greater flexibility and collaboration among teams. Embracing technological advancements in accounting can lead to increased efficiency, reduced errors, and improved financial control in manufacturing operations.
7. How do manufacturing businesses handle depreciation of equipment in accounting?
In manufacturing accounting, handling the depreciation of equipment involves systematically allocating the cost of tangible assets over their useful lives. This process reflects the wear and tear, ageing, or obsolescence of machinery and equipment used in production. Depreciation is recorded as an expense on the income statement, reducing taxable income and providing a more accurate picture of the company's financial performance.
Common methods of depreciation include straight-line, declining balance, and units of production. Selecting the appropriate depreciation method depends on the nature of the equipment and its usage patterns. Properly accounting for depreciation ensures compliance with accounting standards and helps in planning for future capital expenditures.
8. What are the tax considerations unique to manufacturing businesses?
Manufacturing businesses face unique tax considerations, including eligibility for specific tax credits and deductions. For instance, many jurisdictions offer Research and Development (R&D) tax credits to encourage innovation within the manufacturing sector. Additionally, capital allowances may be available for investments in machinery and equipment, allowing businesses to deduct a portion of these costs from their taxable income.
Manufacturers must also navigate complex VAT regulations, especially when dealing with international supply chains. Engaging with tax professionals who specialise in manufacturing can help businesses identify applicable tax incentives, ensure compliance, and develop strategies to minimise tax liabilities effectively.
9. How can manufacturing businesses ensure compliance with financial regulations?
Ensuring compliance with financial regulations in manufacturing involves implementing robust internal controls, maintaining accurate financial records, and staying updated on relevant laws and standards. Regular internal and external audits can identify potential compliance issues and areas for improvement.
Training staff on regulatory requirements and fostering a culture of accountability also play crucial roles. Utilising compliance management software can streamline monitoring and reporting processes.
Non-compliance can lead to severe financial penalties and reputational damage, making it essential for manufacturers to adopt proactive compliance strategies to mitigate risks and maintain financial integrity.
10. What are the risks of managing accounts internally in a manufacturing business?
Managing accounts internally in a manufacturing business carries several risks, including errors in financial reporting, misallocation of costs, and potential non-compliance with tax laws. Without the expertise of professional accountants, businesses may struggle to track inventory accurately, leading to inefficiencies and financial losses.
Internal teams may also lack the time or resources to stay updated with changing accounting standards and regulations, increasing the risk of legal penalties. Additionally, inadequate internal controls can result in fraud or financial mismanagement.
Outsourcing accounting functions to experienced professionals can help mitigate these risks, ensuring accuracy, compliance, and strategic financial planning.
11. How can an accountant help you avoid these risks?
An accountant with expertise in manufacturing accounting can help businesses avoid financial risks by implementing accurate bookkeeping practices, ensuring proper cost allocation, and maintaining compliance with tax regulations.
They provide financial insights that aid in strategic decision-making, such as cost reduction and pricing strategies. Accountants also conduct regular audits to detect errors and prevent fraud. By leveraging financial management tools and automation, they enhance efficiency and reduce the likelihood of human error.
Partnering with a professional accounting firm provides peace of mind and allows manufacturers to focus on core business operations while maintaining financial health.
12. Why choose Pulse Accountants for your manufacturing accounting?
Pulse Accountants specialises in manufacturing accounting, offering tailored financial solutions to help businesses optimise costs, improve cash flow, and ensure compliance. Our team of experienced professionals understands the complexities of manufacturing operations and provides strategic financial guidance to enhance profitability.
We utilise the latest accounting technologies to streamline processes, improve accuracy, and deliver real-time insights. Our proactive approach ensures that clients stay ahead of regulatory changes and financial challenges. With
Pulse Accountants, manufacturing businesses gain a trusted partner dedicated to their financial success, allowing them to focus on growth and innovation.
Check out our
Latest insights
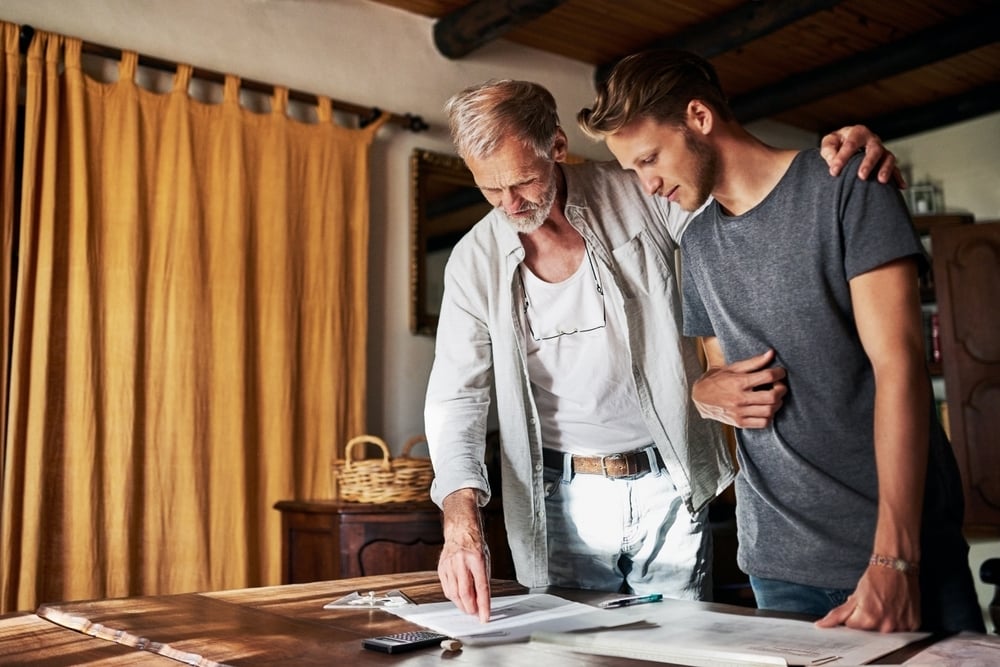
- blog
- Business Advisory
View Article
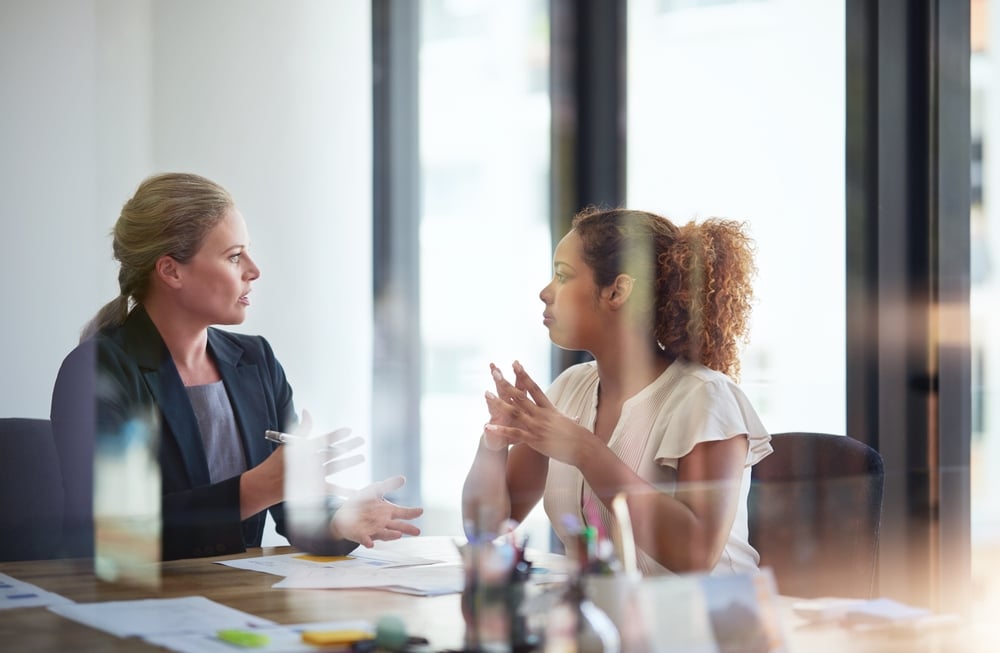
- blog
- Business Advisory
View Article
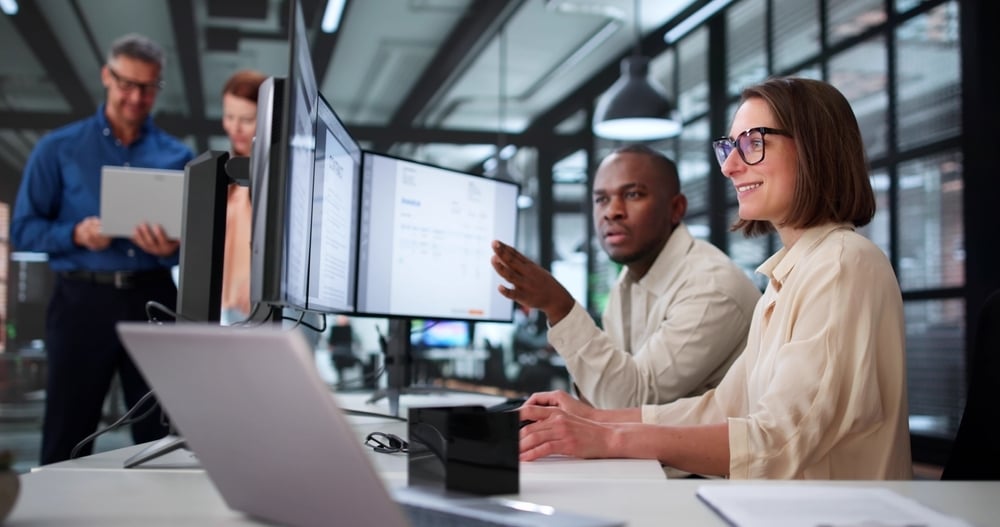
- blog
- Business Advisory
View Article
Frequently Asked Questions
-
Pulse specialises in cost analysis, offering tailored solutions such as activity-based costing, variance analysis, and overhead allocation optimisation to ensure efficient resource utilisation and enhance profitability.
-
We have expertise in inventory management and production planning for the manufacturing sector. Our team will help you implement inventory systems, develop production schedules, and utilise inventory turnover analysis to optimise stock levels and minimise carrying costs.
-
It's one of our specialties. Our accounting service offers advanced financial modelling and forecasting tools tailored to manufacturing businesses. We'll provide you with detailed budget projections, cash flow forecasts, and sensitivity analysis to support strategic decision-making and mitigate financial risks.
-
We provide comprehensive tax planning and compliance services specific to the manufacturing industry. This includes identifying eligible tax credits, optimising depreciation schedules, and ensuring compliance with industry-specific tax incentives and deductions to minimise tax liabilities and maximise savings.
-
We offer specialised financial analysis and strategic planning services to support your expansion goals. From conducting feasibility studies and market analysis to evaluating investment returns and financing options, Pulse will provide you with the insights and support needed to make informed decisions and achieve sustainable growth in your manufacturing business.
Still got questions?